Expert Suggestions on What is Porosity in Welding and How to Resolve It
Expert Suggestions on What is Porosity in Welding and How to Resolve It
Blog Article
Porosity in Welding: Identifying Common Issues and Implementing Ideal Practices for Prevention
Porosity in welding is a prevalent issue that frequently goes unnoticed until it causes significant problems with the integrity of welds. In this discussion, we will explore the key factors contributing to porosity formation, analyze its destructive results on weld efficiency, and go over the finest methods that can be embraced to reduce porosity occurrence in welding processes.
Common Sources Of Porosity
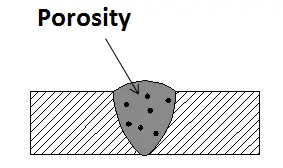
One more constant wrongdoer behind porosity is the visibility of impurities on the surface area of the base metal, such as oil, oil, or corrosion. When these contaminants are not successfully removed prior to welding, they can evaporate and come to be entraped in the weld, creating defects. Additionally, making use of unclean or wet filler materials can introduce pollutants into the weld, adding to porosity issues. To mitigate these usual reasons of porosity, complete cleaning of base metals, correct securing gas choice, and adherence to optimum welding criteria are necessary methods in achieving top notch, porosity-free welds.
Impact of Porosity on Weld Top Quality

The existence of porosity in welding can significantly jeopardize the structural integrity and mechanical properties of bonded joints. Porosity produces gaps within the weld metal, weakening its general stamina and load-bearing capacity. These spaces work as anxiety focus points, making the weld a lot more prone to cracking and failing under used tons. Additionally, porosity can lower the weld's resistance to deterioration and other environmental factors, better decreasing its long life and performance.
Among the key consequences of porosity is a decrease in the weld's ductility and durability. Welds with high porosity degrees tend to display reduced impact stamina and decreased capacity to deform plastically before fracturing. This can be especially worrying in applications where the welded elements undergo dynamic or cyclic loading conditions. Porosity can hamper the weld's capacity to efficiently transfer pressures, leading to see premature weld failing and possible safety and security threats in essential structures. What is Porosity.
Ideal Practices for Porosity Avoidance
To enhance the structural stability and high quality of bonded joints, what details measures can be executed to minimize the occurrence of porosity during the welding procedure? Using the correct welding technique for the details material being bonded, such as adjusting the welding angle and weapon position, can even more stop porosity. Normal evaluation of welds and prompt remediation of any type of concerns identified throughout the welding process are crucial practices to stop porosity and produce premium welds.
Importance of Proper Welding Techniques
Executing proper welding techniques is paramount in ensuring the structural honesty and top quality of bonded joints, building on the structure of effective porosity prevention measures. Welding methods straight influence the overall strength and toughness of the bonded structure. One essential aspect of proper welding strategies is keeping the right heat input. check out here Excessive warmth can cause boosted porosity as a result of the entrapment of gases in the weld swimming pool. Conversely, insufficient heat may cause incomplete fusion, developing prospective powerlessness in the joint. In addition, utilizing the suitable welding criteria, such as voltage, present, and travel rate, is important for achieving audio welds with minimal porosity.
Additionally, the choice of welding procedure, whether it be MIG, TIG, or stick welding, ought to straighten with the particular demands of the project to guarantee optimum results. Appropriate cleansing and preparation of the base metal, in addition to choosing the ideal filler product, are likewise important parts of proficient welding methods. By sticking to these ideal practices, welders can lessen the threat of porosity formation and produce premium, structurally sound welds.
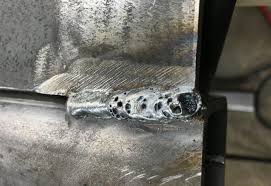
Examining and Quality Assurance Measures
Checking procedures are important to identify and stop porosity in welding, making certain the stamina and longevity of the last item. Non-destructive screening techniques such as ultrasonic testing, radiographic screening, and aesthetic assessment are typically employed to identify possible flaws like porosity.
Performing pre-weld and post-weld assessments is also essential in preserving quality assurance criteria. Pre-weld evaluations involve confirming the materials, tools settings, and sanitation of the workspace to avoid contamination. Post-weld evaluations, on the various other hand, examine the final weld for any type of defects, consisting of porosity, and confirm that it satisfies defined standards. Carrying out an extensive top quality control plan that consists of comprehensive screening procedures and assessments is critical to lowering porosity issues and making certain the total top quality of bonded joints.
Verdict
Finally, porosity in welding can be a common problem that influences the top quality of welds. By identifying the common root causes of porosity and implementing best practices for avoidance, such as proper welding methods and screening actions, welders can make certain premium quality and trustworthy welds. It is essential to prioritize prevention methods to reduce the incident of porosity and have a peek here keep the stability of bonded frameworks.
Report this page